Developing the safety culture
A strong safety culture is an effective tool for improving the Group’s overall safety performance, and is also a key component within OHS management. When developing the corporate safety culture we focus on fostering appropriate attitudes towards safety among all employees, the environments in which people work, and systems and processes related to occupational health and safety. In 2019, we implemented a number of corporate initiatives focusing on employee engagement and empowerment, establishing robust feedback mechanisms, building an integrated training system, further developing the occupational safety risk assessment methodology by introducing new tools and technics, and organising events to improve the corporate safety culture.
Occupational health and safety promotion
For a number of years EVRAZ has carried out effective health promotion activities which assist the Group in adapting appropriate administrative procedures, raising awareness, and helping workers apply safe working practices.
We annually hold the EVRAZ Safety Week, which encompasses various health and safety activities. Employees have an opportunity to get tested for HIV and participate in a quiz on safety practices and procedures. During this week we also hold special corporate conferences and meetings devoted to health and safety.
Other promotional tools include EVRAZ TV, the corporate web portal, and the EVRAZ News newspaper, containing dedicated information blocks on occupational health and safety. In 2019, we also filmed and posted on social media three related videos, which went viral and were nominated in the Cannes Corporate Media & TV Awards. EVRAZ also adopted another popular promotional tool, a social media campaign.
GRI 403-2
Case study
In 2019, as part of efforts to raise safety awareness, we initiated the social media challenge “Zero is also a record!” The challenge consisted of attaining an LTIFR score of zero, and thereby symbolise an aspiration to achieve a work environment without injures.
Around 3,000 people joined the campaign and posted photos on social networks using the hashtag #Iworksafely. During the eight-day campaign a video about the challenge was viewed 622,000 times.
As part of the challenge EVRAZ also funded several operations for critically ill children.
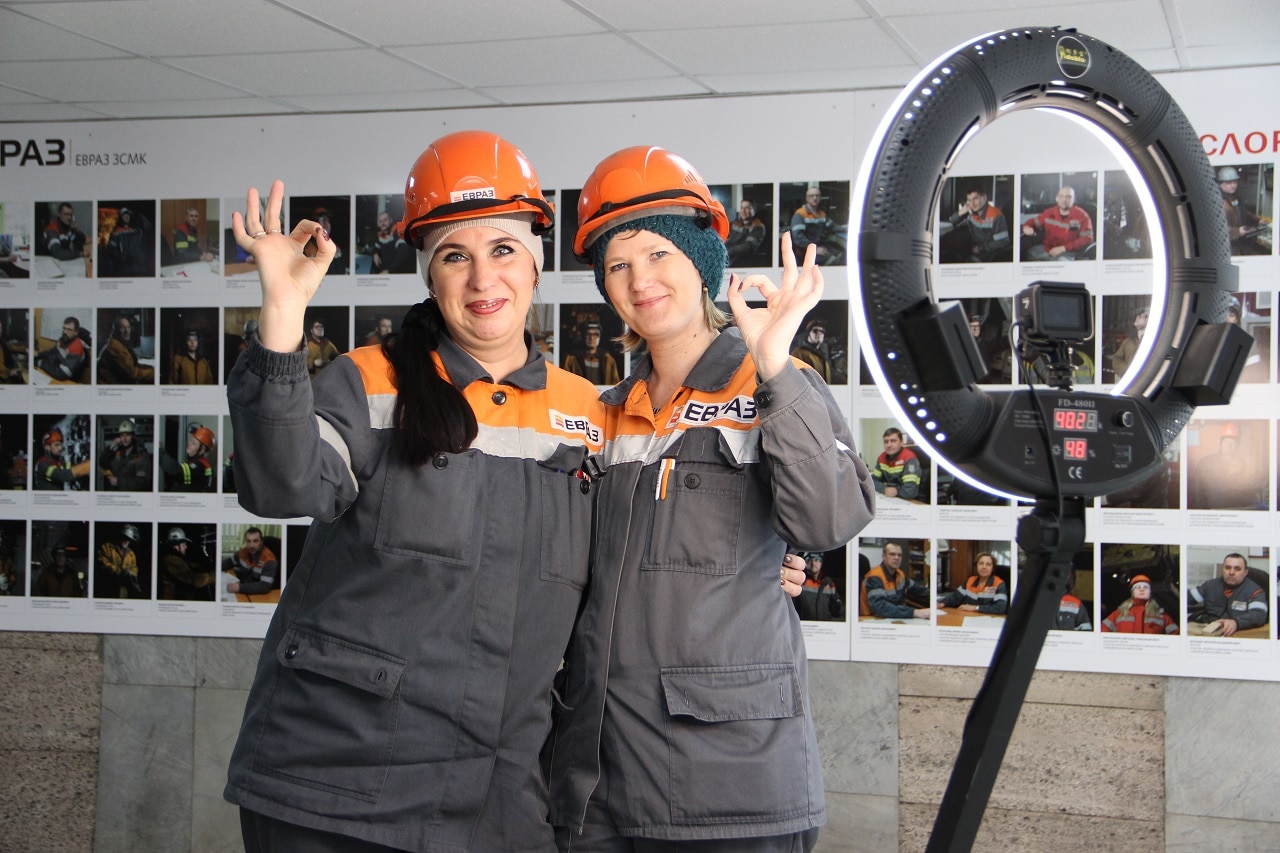
Occupational health and safety trainings
GRI 403-5
The aim of our regular and comprehensive OHS education courses and trainings is to provide employees with the knowledge and skills that they need to perform their work safely. EVRAZ delivers a variety of training programmes and courses in training centres at its business segments. In line with legal requirements, EVRAZ provides one-week health and safety training sessions for employees twice a year. We also regularly monitor and evaluate the skills and knowledge of our personnel in this area. All employees must pass an examination on safety rules and a working instruction. Engineering and technical specialists are certified by special commissions on OHS rules and emergency responses. In addition, all employees must complete a test on emergency procedures after extended periods of leave.
In addition to legally required trainings, EVRAZ provides a variety of programmes, including initiatives on developing of training centres and security systems, working at height and crane work trainings, electrical safety, and a safe driving course.
In 2019, EVRAZ initiated new risk management training programmes as part of the Risk Management project. In addition to newly developed courses, these programmes also include updated trainings aligned with our risk management approach. All EVRAZ employees will undergo the trainings. The Group plans to raise the number of occupational health and safety training hours by 150%, and workers will participate in four-hour in-person and four-hour online training sessions, while line managers will undergo three-to-four-day trainings. In 2019, 300 employees, including from top management, participated in the new training initiative.
EVRAZ completed the lockout-tagout safety awareness training and incorporated the LOTO system. The system is designed to protect personnel from unauthorised equipment activations during repairs. By the end of 2019, the LOTO system had been integrated into 10 facilities in the Siberia region (Steel segment) and at 12 facilities in the Urals region (Steel segment), which gave a 70% integration level.
Behaviour safety conversations and safe work procedures
GRI 403-7
Measures related to improving the safety culture and further engaging employees in OHS management are among the key success stories of the Risk Management project. A critical role in improving safety performance is played by efficient interactions between a worker and a line-manager, including further developing the behaviour safety conversations tool.
In 2019, the working relationship between an employee and their line-manager was boosted by a new efficient procedure. This is a six-step procedure that helps determine safety risks and streamlines communication channels.
- An employee comes to the workplace
- The employee observes the surrounding environment
- The employee identifies risks to their life and health and to the safety of other workers
- In case of a threat to life or health the employee refuses to perform their work
- The employee reports the identified risks
- The identified risks are properly mitigated
The procedure has also been incorporated into behaviour safety conversations, and facilitates dialogue between employees and line-managers, helps strengthen safety attitudes among employees, and involves employees in the process of improving their working environments.
In line with the Risk Management project another tool, a dynamic risk assessment checklist, has been elaborated and incorporated into daily operations. This tool gives employees brief and clear instructions on when and how risk identification should take place, and also lists respective actions to be taken.